Plunger vs. Diaphragm Pump: How to Choose the Best Pump

Shawn Glover, VP of Sales, Mar 28, 2023
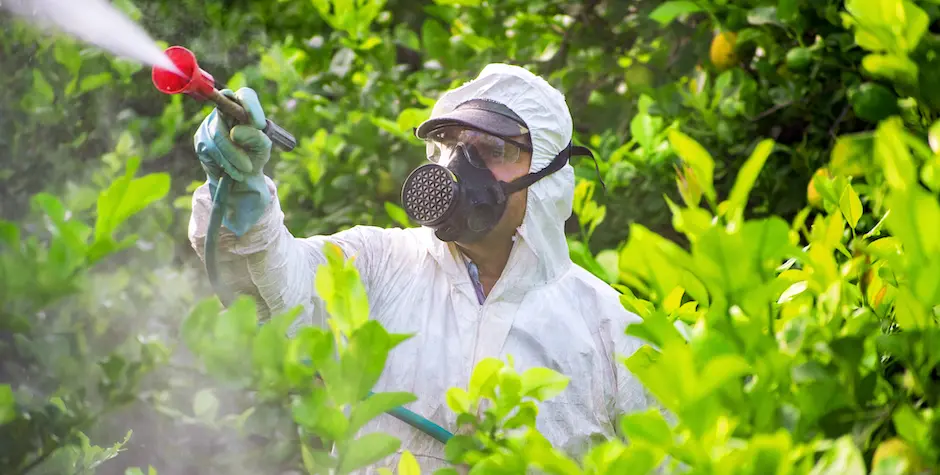
What’s the difference between plunger and diaphragm pumps? And how can you know which type of pump is best for commercial pump equipment and applications?
Both are considered positive displacement pumps, but there are stark differences in performance and where each is best suited. While some manufacturers configure both types of pumps into various equipment models, they’re not necessarily interchangeable without some compromises.
Here, we’ll give a brief, simple explanation of how each pump design works. Then, we’ll outline the pros and cons of plunger vs. diaphragm pumps and how to know which one is best for your equipment.
How Do Plunger Pumps Work?
Plunger pumps have a reciprocating plunger or piston that moves back and forth, forcing liquids through a set of valves. Some simple examples in our everyday lives might include a bicycle pump, spray bottle, or squirt gun.
Commercially, plunger pumps are commonly used in soft wash, portable sanitation, disinfection, pest control, agriculture, and other high-pressure applications. They can be configured into electrically powered equipment such as pressure washers, misters, and sprayers.
How Do Diaphragm Pumps Work?
There are similarities between plunger pumps and diaphragm pumps. Both are reciprocating pumps. However, the end of the plunger in a diaphragm pump is connected to a flexible diaphragm that flexes back and forth. The human heart, for example, is a type of naturally occurring diaphragm pump.
Commercially, however, they are commonly used for dewatering and transferring fluids and are best when used for lower PSI. Some commercial manufacturers configure them into spray equipment, but they are not always suited for such uses.
The Pros & Cons of Plunger and Diaphragm Pumps
A notable difference between plunger and diaphragm pumps is their power source. A diaphragm pump can be manufactured to accommodate a gas-powered engine or electric-powered motor. However, a gas-powered diaphragm pump is required to achieve the desired output and power needed for most professional uses. Electric diaphragm pumps are typically sold for residential use in small hand-held sprayers, RV sinks, and other low-impact uses.
Commercial piston and plunger pumps are available as 12V battery-powered or gas powered units. Unlike diaphragm pumps, however, manufacturers like Pumptec can engineer their electric battery-powered plunger pumps to perform as well or better than gas-powered diaphragm pumps in rugged, commercial applications.
For the purpose of this article, we’ll compare commercial electric plunger pumps to gas-powered diaphragm pumps in the following areas.
- Spray Patterns and Flow
- Priming
- High-Pressure Capabilities
- Noise Levels
- Run Times
- Size
- Environmental Impact
- Cost
Spray Patterns and Flow
Plunger pumps have a stable flow by use of a pressure regulator. Liquids are dispensed through the plunger pump system at a steady, fixed flow rate due to rigid components. Operators can achieve consistent, even coverage.
Diaphragm pump components are flexible, so the flow is also “flexible.” They’re notorious for losing pressure and having inconsistent spray patterns. This is a major concern for pumps that use harsh chemicals in highly regulated industries like fertilizer applications, soft wash, disinfection, and others.
Priming
Unlike a centrifugal pump which requires priming to remove air from the pump chamber and avoid becoming inoperable, both the plunger pump and diaphragm pump will self prime.
RELATED: The Pros & Cons of Self-Priming Pumps
High Pressure Capabilities
The flexible components in a diaphragm pump can be its downfall, especially for applications requiring high PSI. The flexible diaphragm can rupture under higher pressure over time whereas a plunger pump is engineered to withstand repeated high-pressure use. If you’re constantly issuing refunds or warranty replacements for diaphragm pumps used in your high PSI equipment, you may simply need to switch to a more durable plunger pump.
Noise Levels
Equipment that uses 12V motors are much quieter than gas engines. If you’re in the pest control industry and your clients don’t want to call attention to the services you provide, a 12V pump system will quietly do the job.
Quiet operation also benefits soft wash and lawn care professionals by increasing the hours of available service. Noise ordinances can limit the hours that gas engine diaphragm pumps can be operated. A 12V plunger pump system would not be affected by such restrictions.
RELATED: Pump Noise Levels & Causes: What You Need to Know
Run Times
Battery technology has advanced significantly in recent years. Today’s 12V plunger pump systems use batteries that outlast the capacity of many gas-powered diaphragm pump engines. The operator doesn’t have to stop in the middle of a job to refuel, and safety is improved by not having to transport volatile substances.
Battery technology aside, the main reason an electric plunger pump competes with a gas-powered pump is because the plunger pump is inherently more efficient. Operators can go an entire day on a single charge and even recharge batteries while driving between jobs.
RELATED: The Importance of High-Pressure Pump Efficiency
Size
Battery-powered units are more compact and maneuverable than gas-powered diaphragm assemblies, making jobs less taxing on operators and improving safety. If you’re looking for a pump with a smaller footprint that can more easily fit in your equipment, the plunger pump wins out. Plunger pump batteries are comparable to a marine battery and are about the same size.
Environmental Impact
Battery-powered 12V equipment offers the benefits of ‘green’ technology. Concern over volatile gas prices, oil dependency, and pollution will continue to rise, and the latest 12V plunger pump technology is an environmentally responsible power source.
Electric plunger pumps also comply with legislation in states where gas-powered small off-road engines are being banned. Sensing the trend will continue, proactive equipment manufacturers are already designing equipment to meet the demand for electric high-pressure pumps in these states.
Cost
Gas engines typically cost more than batteries, and operators also need to purchase fuel on an ongoing basis. Batteries can be recharged again and again and are generally price-stable.
While a diaphragm pump unit might have a lower up-front cost, a battery-powered plunger pump will likely deliver a significantly lower cost of ownership. Not only will equipment manufacturers receive fewer complaints and warranty claims, but operators can limit fuel consumption and have fewer breakdowns, repairs, and downtime.
And the Winner Is…
For high-pressure commercial applications, an electric-powered plunger pump is the most reliable and value-driven option. There are several other types of pumps in the industry, too. Learn about seven of the most common in our Pump Comparison Cheat Sheet below.