Rotary Vane Pumps vs. Plunger Pumps for Mosquito Misting Systems

Shawn Glover, VP of Sales, Apr 5, 2022
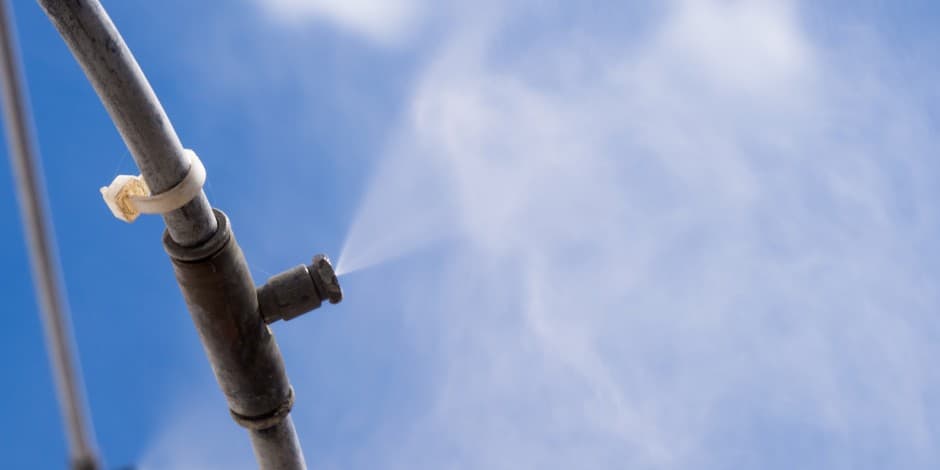
Mosquito misting systems are used in both residential and commercial outdoor settings to help kill or repel flying pests. The use of pesticides is highly regulated, however, and improper use can have a devastating toll on the environment and human health.
Part of the responsibility of using pesticides includes ensuring that the pump equipment dispersing them is operating properly and right-sized for the application. The most common types of high-pressure pumps used for mosquito control are rotary vane pumps and plunger pumps, but there are key differences that should be considered when engineering a mosquito misting pump system.
How Do Mosquito Misting Systems Work?
Before we cover the difference between rotary and plunger pumps, it’s important to distinguish how a mosquito control system operates. Conventional mosquito misting systems include tubing and nozzles that are strategically routed around a treatment area, and are connected to a pump and reservoir containing insecticides like pyrethrins.
The pump is usually positioned on top of a reservoir — typically a 55-gallon tank — and pushes a pesticide mixture out through the tubing and nozzle system where it is sprayed into the air. Some systems forgo a large reservoir and use a tankless dosing or chemical injection system which automatically dispenses and mixes an appropriate amount of pesticides with a water source at the time of operation.
A mosquito misting system operates similarly to a sprinkler system, only it uses an ultra-fine mist with much smaller droplet sizes. These units are usually programmable, spraying at certain times of day like early morning or early evening when mosquitoes are most active. They may also allow for manual operation with the push of a button.
Rotary Vane Pumps vs. Plunger Pumps
Rotary vane and plunger pumps are both positive displacement pumps, and either can get the job done when it comes to mosquito control, but there are some key differences in their operation and upkeep that makes one more suitable over the other. First, let’s identify how each works.
How a Rotary Vane Pump Works
A rotary vane pump has vanes that look like fins. These vanes are attached to a rotor that is slightly offset from the center of a pump cavity. The vanes rotate at extremely high speed inside the pump cavity (up to 1,750 RPM) creating a centrifugal force that pulls liquid into the pump from a larger inlet, trapping it between the vanes and carrying it to the smaller outlet where it exits through a port.
How a Plunger Pump Works
A plunger pump — sometimes called a piston pump — uses a reciprocating plunger, creating a vacuum that draws fluid from the inlet valve and forces it out through the outlet valve. Unlike rotary pumps which use rotational force to displace fluids, piston and plunger pumps use a back and forth motion to move fluid from one end of the pump to the other.
Now that we’ve identified how each pump moves liquids from a reservoir tank and out through a tubing system, let’s cover a few key differences and why our pump experts consider high-pressure plunger pumps to be a better choice for misting systems in general.
Pump Amperage and Horsepower
One of the main advantages of a plunger pump vs. rotary vane pump is that it operates much more efficiently. Some rotary vane pumps operate as low as 30% volumetric efficiency at full load. Comparatively, plunger pumps can run at 90–93% efficiency, which is very important when considering amp draw and motor size.
A plunger pump can operate at only 1.5 amps (⅛ HP) whereas a rotary pump draws about 5.5 amps (½ HP) for most pest applications. If an end user has a dedicated 15 amp circuit and needs to plug in appliances or other units that draw higher amperages, tripping a breaker can become a major issue. The motors for the rotary vane pump need to be tremendously oversized to compensate for the inefficiencies in pump design. As noted above, you need a motor with nearly 3 times more horsepower to get the same performance as the plunger pump.
PUMP RECOMMENDATION: 114T Series Pump with 120 Volt M70 Motor
Power Options
Because of its greater efficiency, a plunger pump is much more suited to operate using solar power if the need arises. This is important for remote locations that don’t have easy access to the electrical grid. The higher amperage of a rotary vane pump could possibly drain a solar-powered system before it has a chance to recharge, causing the nozzles to sputter and fail to properly dispense chemicals.
Energy efficiency and pump sustainability are increasingly important to consumers, and a plunger pump helps support those initiatives.
Compact Size
For the same GPM and PSI ratings, plunger pumps are considerably smaller than rotary vane pumps. The standard motor for the commonly used rotary vane pump measures roughly 10.5”L x 6.25H x 6.87W. A compact plunger pump that achieves the same performance measures 8.61”L x 3.84”H x 7.25”W.
Size is important when fitting a pump onto a mosquito control system as your real estate is typically limited to the top of a 55-gallon drum. The smaller plunger pump unit can be more discreet and will fit more easily into a protective housing. It also makes it easier to install and maneuver.
RELATED CASE STUDY: BATTLING WHAT BUGGED TERMINIX
Serviceability and Maintenance
Durability and reliability are crucial aspects of pump performance, especially with highly regulated industries like pest control. While a pump should never be allowed to run dry, a plunger pump can withstand running dry for short periods of time without damage. A rotary vane pump, however, will quickly fail if allowed to run dry.
If damage occurs, the cost to rebuild a rotary vane pump can be equal to the cost of the pump itself. A plunger pump, like those made by Pumptec, can be restored to new for a fraction of the cost of the complete pump head. Additionally, to restore a Pumptec plunger pump to new takes nothing more than a 3/16” hex wrench and 20 minutes, no matter your experience level.
On the other hand, to restore a rotary vane pump you will need a wrench, rubber mallet, 7/8” socket, bearing puller, and a needle nose pliers. The repair will take at least 45 minutes to an hour depending on your experience level.
Cost
When trying to determine the cost difference between rotary vane and plunger pumps, it’s important to consider the total cost of ownership. When taking a pump’s lifespan, electrical efficiency, ease of maintenance, and versatility into consideration, a plunger pump will outperform a rotary vane pump on both performance and price.
Talk with a pump expert at Pumptec today to explore how our custom plunger pumps can help transform your pest control operations. Our engineers can customize a solution that eliminates the pesky issues you might experience with rotary vane pumps. Want to see side-by-side comparisons of how plunger pumps match up against other types of pumps? Download our Pump Comparison Cheat Sheet below.