Centrifugal Pumps vs. Positive Displacement Plunger Pumps

Shawn Glover, VP of Sales, May 25, 2021
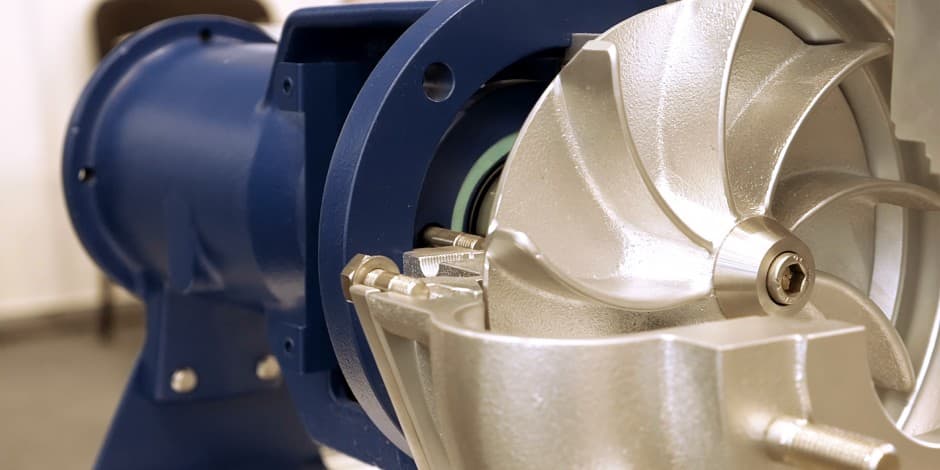
Centrifugal pumps and positive displacement plunger pumps both have their places in the pump industry. But there are significant differences between how they operate and the applications where each will perform best.
Here’s a straightforward explanation outlining how they work, the unique features of each, and the pros and cons of positive displacement plunger pumps vs. centrifugal pumps.
How Does a Centrifugal Pump Work?
A centrifugal pump uses a rapidly rotating impeller powered by a motor, creating a centrifugal force that pushes fluid through the pump system and out a discharge port.
Pros and Cons of Centrifugal Pumps
Centrifugal pumps are best suited to applications requiring large volumes of liquids and high flow rates with relatively low viscosity and low pressure. They are desirable for their simplicity, having fewer parts. As a result, they usually cost less than a plunger pump of the same size, however, there are some disadvantages of centrifugal pumps.
Viscous liquids are typically unsuitable for centrifugal pumps which can limit their uses in some industries. They also require priming or need to be positioned beneath the fluid level to operate properly because they have almost no suction power when full of air.
Flow rates are affected significantly by discharge pressure and cavitation commonly occurs with centrifugal pumps, a phenomenon caused when air bubbles or cavities form in the liquid surrounding the impeller. This is typically associated with low pressure around the impeller and can cause significant damage to the pump. Also, centrifugal pumps should never run dry as it can ruin the shaft seals.
Centrifugal Pump Uses and Applications
Industrial applications with large fluid volumes are common uses for centrifugal pumps, including:
- Municipal wastewater management
- Drainage and irrigation systems
- Power generation plants
- Submersible pumps that do not require priming, such as sump pumps and wells
How Does a Positive Displacement Plunger Pump Work?
A plunger pump uses a reciprocating plunger or piston that moves up and down within the system, creating suction that forces liquids through a set of valves within the pump.
Pros and Cons of Plunger Pumps
Plunger pumps are best suited for high-pressure pump applications that require precise flow rates and consistent PSI. Despite having higher pressure, they can remain compact and portable. Plunger pumps are self-priming, meaning they do not require this step with each use when operated above or below the fluid level.
Depending on the manufacturer and materials used, plunger pumps can be more durable than centrifugal pumps. While never ideal for any pump, plunger pumps can run dry for short periods of time without damaging internal components.
Plunger pumps have more components than centrifugal pumps. As such, the price of plunger pumps may be higher than centrifugal pumps of comparable size. They are not intended for use with fluids that contain a lot of particulates.
Plunger Pump Uses and Applications
Use compact plunger pumps for commercial applications that require precise and consistent flow rates, including:
- Mobile disinfection pump systems
- Chemical injection and metering
- Commercial cleaning and mobile sanitation
- Soft wash, including mold remediation
- Pest control, lawn care, and fertigation
- Misters for evaporative cooling, dust suppression, greenhouses, etc.
- Hydrostatic testing of sprinkler systems, sewer lines, fire hoses, etc.
There are several other types of positive displacement pumps, each with their own unique benefits and drawbacks. We’ve developed a helpful Pump Comparison Cheat Sheet that outlines seven different kinds of pumps and their pros and cons. Access the guide below.
It’s critical to choose the right pump that is designed for your application. As a manufacturer of made-in-America plunger pumps, Pumptec is here to answer questions about your unique application and address any challenges you may face. Reach out to us for a free consultation.