Plunger Pump vs. Piston Pump: Is There a Difference?

Shawn Glover, VP of Sales, Jul 26, 2022
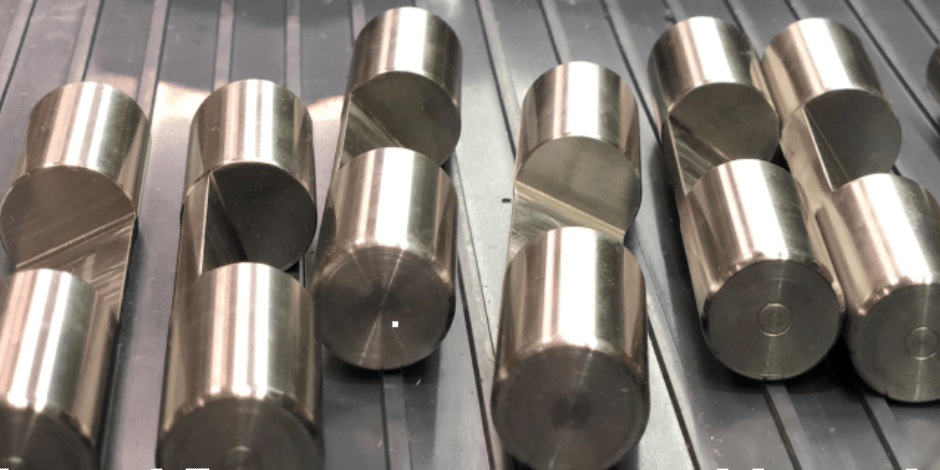
There are a lot of people who use the terms piston and plunger pump interchangeably. Granted, they are both positive displacement pumps and there are similarities, but their subtle differences are kind of a big deal when it comes to an operator’s desired performance, price, and pump longevity.
So, what is the difference between plunger pumps vs. piston pumps and why does it matter? Let’s start with the short definitions.
What is a Plunger Pump?
Plunger pumps have a reciprocating plunger (a type of rod). When it moves back and forth, it sucks liquid in through an inlet valve and forces it out the outlet valve. Plunger pumps have a stationary, high-pressure seal that is attached to the cylinder housing of the pump.
Plunger Pump
What is a Piston Pump?
Piston pumps also have a reciprocating rod called a piston that moves back and forth to force liquid through a set of valves. Unlike a plunger pump, however, a piston pump’s seal is connected to the piston, meaning it moves in unison with the piston inside the cylinder housing.
Plunger (left) vs. Piston (right)
What’s the Difference Between Piston and Plunger Pumps?
From an engineering standpoint, it’s easy to understand that the main difference between piston and plunger pumps is the placement of the seals or O-rings. Again, the plunger pump’s seal is stationary while the piston pump’s seal moves with the piston.
But how do those differences affect the performance of the pump? Turns out, it can have a significant impact in the following areas.
Pressure Capabilities
When a reciprocating rod goes back and forth within either a piston or plunger pump, you have to seal it against the cavity wall so that it doesn’t lose compression. Because the seals of a plunger pump are not attached to a rod, it allows for less friction and higher pressure output. When the seal is connected to the moving part, as with a piston pump, the dynamic sliding action occurs along the walls of the housing, resulting in less pressure.
Here’s why. When a piston pump pushes a rod with an attached seal forward, you get friction that pushes back against the seal. Friction makes the seal want to react in the opposite direction of the motion, making the pump have to work harder to achieve more pressure.
A plunger pump has a smoother sliding action. Translation: less friction. In a plunger pump where the reciprocating rod doesn’t have an attached seal, the friction is in the same direction as the movement of the plunger. But the pressure is in the opposite direction, meaning they help to cancel each other out to some degree. Reduced friction means the motor doesn’t need to work as hard to achieve higher pressures.
Pump Materials and Durability
Design for Manufacturability (DfM) comes into play when determining the durability of a pump’s design, especially in regards to which materials can be used where.
The material makeup of a pump’s housing and the reciprocating plunger or piston will have the greatest impact. In general, you want the component that has the greatest potential for wear to be as hard as possible to avoid scratches and a broken seal.
Common materials used in the pump industry include anodized aluminum, stainless steel, and brass. But the hardest available material used in some pump designs is ceramic. It doesn’t wear out over time like most metals, plus it has great chemical compatibility. It can be polished to a very consistent and smooth surface finish which is perfect for creating a tight seal.
The only problem is that ceramic has very strong compression strength and poor tensile strength. Strong compression will resist being pushed against whereas strong tensile properties resist being pulled apart or bent. It’s similar to concrete which is extremely strong, but try to bend it and it will crack.
Why does this matter? In a plunger pump, it’s the plunger that needs to seal against the cavity wall, meaning it should be the hardest material possible. In a piston pump, it’s the cavity walls that need to seal against the rod with the O-ring, meaning the cavity wall needs to be as strong as possible.
However, engineering and fabricating a thin, tube-like cavity wall out of ceramic or other material and making the inside of it perfectly smooth and consistent is a much greater challenge than fabricating the exterior of a perfectly smooth plunger out of those same materials. Even if it were possible to make the internal housing walls out of ceramic, its poor tensile strength would quickly lead to cracking and pump failure.
In other words, it’s much easier to make the plunger out of hard materials than it is to make the housing out of those same materials. As a result, plunger pumps can be engineered to be much more durable than piston pumps.
RELATED: Pros and Cons of Ceramic vs. Stainless Steel Plunger Pumps
Maintenance
Many piston pumps require an oil bath. Some versions also have a second oil reservoir or oil pan with a wick to lubricate the backside of the piston seal. These reservoirs need to be refilled and maintained if you want to keep the pump operating as it should.
Many plunger pumps, like those manufactured by Pumptec, have oil that is contained in a sealed chamber and do not require draining or refilling of any oil reservoirs.
RELATED: Triplex Oil Bath vs. Sealed Bearing Pumps: What’s the Difference?
The more parts you have, the more maintenance is required. Plunger pumps have a relatively simple design, fewer parts, and require much less maintenance than piston pumps. Simply put, there’s less that can go wrong with a plunger pump.
Pump Costs
What else results from fewer parts and a simpler design? Lower cost. Plunger pumps, in general, can have considerably lower up-front costs than piston pumps when comparing similar performance. Their total cost of ownership is typically less, too, especially when you factor in maintenance, repairs, or replacement over time.
If you haven’t guessed by now, we’re a bit biased toward plunger pumps. Many of the reasons stated here are why our company ventured into the industry in the first place: we saw the need for better durability and performance at a fair price point.
If you’re in the market for high-performance, high-pressure electric commercial pumps for your industry application, get in touch with our team of pump experts. We’re happy to talk through your needs and challenges to determine a solution.
Curious about some of the terms used in this article? We developed a helpful Pump Terms Glossary with common terms and relevant information. Click below to download your copy today.