Pump Assembly vs. Standalone Pump: Cost Comparison

Shawn Glover, VP of Sales, Sep 6, 2022
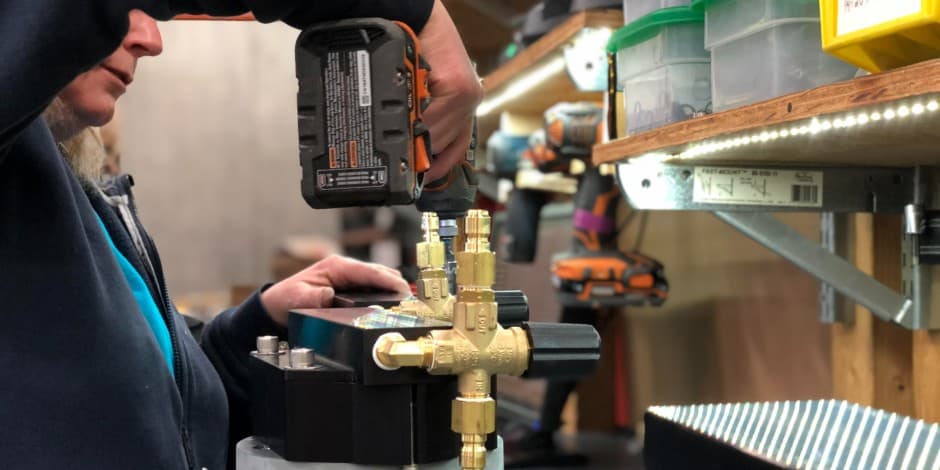
Cost is always a top consideration when deciding which electric high-pressure pump to use when manufacturing a piece of equipment.
But is it more cost effective for manufacturers or users of such systems to invest in a complete “plug-and-play” pump assembly? Or is it better to use a standalone pump and configure all the fittings and plumbing on their own?
There’s no doubt that the up-front cost of a pump assembly is more than just the pump alone. However, many OEMs are surprised to find that when they really do the math, the pump assembly comes out ahead on both price and performance in the end.
Let’s start with the basics by identifying the parts of a pump assembly and some critically important attributes of those components. That will guide the conversation about costs and whether it’s better for an OEM’s bottom line to invest in the complete pump assembly versus just the pump itself.
What is a Pump Assembly?
A pump assembly includes all the components necessary for the pump to operate and is custom designed and manufactured to fit inside the intended equipment.
Components typically include the:
- Pump
- Electric motor
- Regulator
- Pressure gauge
- Hoses
- Fittings
- Plumbing
- Mounting brackets
Typically, the equipment manufacturer is only responsible for bolting down the assembly unit and hooking up the hoses.
Important High-Pressure Pump Assembly Considerations
Using a pump assembly that’s specifically designed for a piece of equipment helps to overcome many manufacturing challenges and potential problems. In particular, the types of components need to be carefully selected and configured in a way that optimizes pump performance. Components can’t simply be purchased off a hardware store shelf or out of a catalog without a deep knowledge of how they’ll perform on a given pump.
To start with, the type of hose and its rigidity matters. If the inlet hose is too rigid, it can result in air bubbles getting sucked into the pump which then burst, creating excessive vibration and shock. These air pockets are what lead to cavitation in pumps, damaging the pump head and valves. On the other hand, if the hose is too malleable and soft, it can collapse and restrict flow. Determining the appropriate rigidity of a hose can’t be left to guess; it needs to be suitable for the pump’s rated GPM and PSI.
For outlet hoses used at high pressure, we typically recommend pulse hoses. Lower pressure applications around 150 PSI can use a general ag hose. Outlet hoses should be soft and absorbent to minimize pulsation, providing smoother performance and further reducing the risks of cavitation.
Also consider the size of hoses. An inlet hose that is too small won’t allow enough fluid through the system and reduce performance. If the hose is too large, the pump will draw in air or trigger the regulator into bypass mode. For most Pumptec pumps, we generally recommend a ¾-inch bypass line. Going any smaller might not allow fluid to evacuate fast enough and could burn out the motor.
In addition to the hoses, fittings and plumbing need to be properly configured. We’ve seen too often how excessive use of 90° elbows, brass fittings, commodity components, and improper positioning of reservoirs can set a manufacturer up for pump failure and cavitation. Pump engineers have a keen knowledge of fluid dynamics and understand how improper plumbing configurations can negatively impact a pump’s performance and longevity.
There are also a lot of aftermarket regulators that shouldn’t be used on certain pumps. Many of them come with design flaws or aren’t intended for use on pumps rated at a specified GPM and PSI. Allowing the pump manufacturer to design and install a properly fitted and rated regulator helps ensure it will work as intended.
There are a lot of small yet important pump details that might escape notice by someone who isn’t familiar with pump engineering and fluid dynamics. Allowing the pump manufacturer to design and manufacture the assembly so that it aligns with the chosen pump can eliminate a lot of costly issues down the road.
At Pumptec, we conduct numerous tests and pressurize each pump assembly to its rated performance (up to 1200 PSI) to ensure the hose is properly matched to the system and that all fittings, plumbing, regulators, and other components operate as they should before heading out the door. We mimic the environment in which the final assembly will perform. One example of such an environment might be whether the pump’s suction needs to lift fluid from a reservoir below or be gravity fed. This can have a major impact on performance, and an assembly can be modified to address the issue.
Providing a complete system that is tested to the manufacturer’s exact specifications helps take out the guesswork on the assembly line and in the field.
RELATED: How to Configure a Plunger Pump Into a System
Cost Comparison of Pump Assembly vs. Standalone Pump
All of these factors lead into the discussion of cost. Understandably, some manufacturers might want to save a few dollars by simply purchasing a pump and all the components separately. But a deep dive into the associated ancillary costs often reveals that a customized pump assembly is less expensive in the long run.
In manufacturing, time is money. The ability to simply drop a completed, ready-to-go pump assembly into a manufacturer’s equipment design helps streamline efficiencies and improve speed to market. Take, for example, something as simple as a hose. That single component would require multiple touchpoints throughout a facility: procurement, vendor management, receiving, inventory SKUs, routing, prep, measuring, cutting, installing, inspecting, etc. The overall cost of that simple hose suddenly becomes exponentially more than the catalog price. Furthermore, there’s no guarantee it will be the proper hose for the application in the end.
Now consider that each of those touchpoints needs to be replicated for every component mentioned above. The cost of labor alone far outweighs the cost of having a custom-engineered pump assembly that’s tailored to a manufacturer’s specifications. Additionally, knowing that they won’t have to worry about pump failure or troubleshooting will lead to fewer returns and repairs, higher end user satisfaction and loyalty, and better customer lifetime value.
Steps to Determining Pump Assembly Costs
At Pumptec, we work closely with manufacturers of pump equipment for numerous commercial industries, including soft wash, commercial cleaning, agriculture, pest control, disinfection, portable sanitation, chemical metering, hydrostatic testing, and a host of others. These diverse industries require diverse pump assembly configurations, so we customize assemblies to work with an OEM’s design.
To explore how cost-effective these solutions are, speak with one of our pump experts who will help you determine pump assembly pricing for your equipment’s design and intended use.
There are also four assembly kit solutions that our engineers designed to work with common pump system configurations like those for hard-surface cleaning, hobby farming, pest control, and power washing. View those options on our website and reach out with questions.
It’s well worth it to explore including a customized pump assembly in your equipment. To further understand what goes into configuring a pump into a system, be sure to check out our helpful guide below.