Pulse Hose Benefits in Pump Systems

Shawn Glover, VP of Sales, Mar 2, 2021
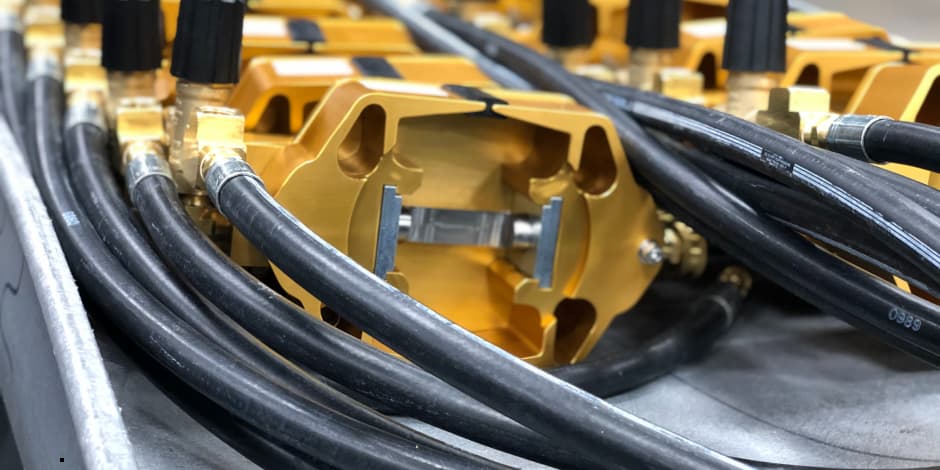
Pulse or pulsation is an integral part of every reciprocating pump system. Despite this inherent characteristic, it’s important to control pulsation in pumps to provide optimal performance.
While check valves, pulsation dampeners, and proper pump design and engineering can minimize this natural phenomenon in pumps, the addition of pulse hoses can also help provide smooth operation, accurate flow rates, and prevent unnecessary wear and tear.
What is a Pulse Hose?
A pulse hose is a specially manufactured hose that, unlike a typical hose, will expand slightly to dissipate energy and built-up pressure. The energy dissipation quality decreases momentary pressure spikes and smooths flow and performance. A pulse hose is installed between the outlet of a pump system and the control panel or the hose reel quick connect that extends to the spray gun.
What is Pump Pulsation?
Many operators are familiar with the signature sound of pump pulsation in a pressure washer pump or other pump application: an unmistakable chatter or vibration during operation. These noises come from the hydraulic pulsations vibrating in the pump and motor, and other system components vibrating in the equipment case.
But what causes pump pulsation? Each compression cycle of a pump creates a pressure spike followed by a pressure drop. If the pressure spikes are not dissipated, system components receive the spikes and can cause premature wear, noise, lower performance, and higher energy needs.
Pumps with higher flow rates generally have more pulsation. Contrary to popular belief, pulsation is not a result of the pressure itself; flow change is what causes pressure spikes. Imagine a pump chamber with a piston that goes back and forth, pushing fluid in and out. Every time the piston changes direction, there’s a momentary pause. It’s this sudden pause that creates pulse. A pump with a higher flow rate requires more distance between starts and stops, resulting in more pulsation.
Will Pulsation Damage a Pump?
Pulsations can compromise a system over time. There are several pump components that are affected by pulsations:
- Gauges can fatigue from the pulsations and fail prematurely
- In-line heater coils can become stressed and crack, requiring replacement
- Regulators can experience premature seal failure from the frequent bouncing of the regulator piston with each pulsation
Lower performance results from the regulator piston bouncing and allowing fluid to bypass out and not go through the nozzle to create pressure. To compensate for the lower performance, the pressure is often adjusted higher resulting in higher energy requirements during spray and bypass.
Do Some Types of Pumps Have Less Pulsation?
The components of a plunger pump are more rigid than some pumps, making them less prone to pulsation problems. Diaphragm pumps, on the other hand, feature flexible components, which can lead to pressure loss. The pump then needs to overcompensate, creating pressure spikes. These inconsistencies can make a pump more prone to pulsation and inconsistent flow, and are more prone to damage from pulsation.
RELATED: What’s the Difference Between Plunger Pumps vs. Diaphragm Pumps?
In the case of a plunger pump, also known as a piston pump, the reciprocating plunger moves back and forth rapidly, pushing liquids through the system. Pulsation can occur when there is acceleration and deceleration of energy and fluid becomes trapped. Once that energy is released or absorbed, the pulsation stops.
This chart shows the pulsations of a Simplex pump with one plunger.
This chart shows the pulsations of a Duplex pump with two plungers.
Right-sizing the pump for your application is the first step in helping to minimize pulsation. Additionally, the more pumping chambers in the pump, the less spikes you’ll have to deal with. A two-plunger pump will have less pulsation than a single plunger pump because they offset each other.
The Role of a Pulse Hose in a Pump System
Using a pulse hose within a pump system is recommended, and the proper length of hose is critical for optimal system performance. Calculating how much pulse hose you need for your pump system can vary. As a general rule of thumb, use the ratio of six (6) feet of total pulse hose for every one (1) gallon per minute (GPM) of flow as a guide.
For example, if you use our 350U pump sprayer in a pest control or lawn care application and you require 2.2 GPM, the recommended pulse hose length would be a little over 13 feet.
Some pump manufacturers suggest the use of pulse dampeners on the output line. There are drawbacks to these pump accessories, however. They can be expensive, and pulse dampeners are big and bulky. This can make it hard to fit in some equipment and be a major disadvantage in applications where mobility is desired. Besides, the system will still need a hose in addition to the dampener, so why not just use a pulse hose and achieve similar results?
The type of pump you use can make a major difference in how well you control pulsation within a system. Certain positive displacement pumps, like diaphragm pumps and peristaltic pumps, can experience high levels of pulsation and inconsistent spray patterns if the pulse and pressure isn’t properly discharged. Because of their design, pressure pulses can be difficult to control.
Diaphragm pumps, in particular, typically require a pressure switch. If you have a small nozzle and increase the PSI, the pump will cycle on and off, changing flow rates and creating a sense of pulsation. This can cause a sprayer to shoot liquids in a pulsating flow, similarly to a machine gun. In this situation, even a pulse hose will do little to solve the problem.
The design of plunger pumps allows for highly variable fluid flow rates, making them ideal for low flow, high pressure commercial applications. The combination of proper design and the use of pulse hoses helps ensure consistent flow and application rates.
Pumptec-designed systems have the proper length of pulse hose to provide optimal performance. As mentioned, flow rates play a critical role in managing pulsation. To help you determine the ideal flow rate, download our Guide to Proper GPM and PSI below.
If you’d like to solve for pulsation problems or any other pump challenges, be sure to speak with our pump experts. They’ll help you find the right pump solution for your application.