Does Your High-Pressure Pump Have the Right Horsepower?

Shawn Glover, VP of Sales, Jul 12, 2022
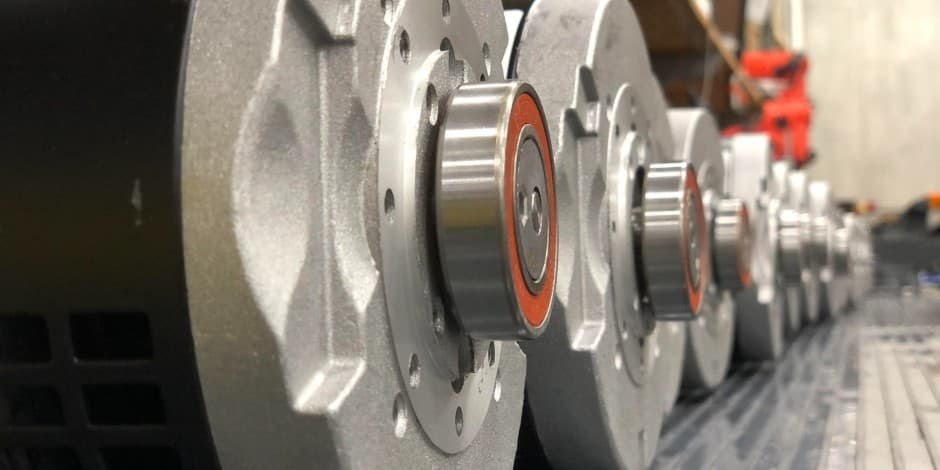
When you consider which high-pressure electric pump is right for an application, there’s a lot of emphasis on getting the proper flow and pressure. And rightly so. Determining proper GPM and PSI is critically important.
But the right flow and pressure can only occur if you have the right motor.
Performance is generally determined by the amount of horsepower in electric motors. What is the role of horsepower and how can you determine how much you need?
What is Horsepower in Electric Motors?
The term horsepower, often abbreviated HP, stems from the 18th century and was coined by Scottish engineer, James Watt. He developed a calculation that compared the power of draft horses to the output of steam engines which were relatively new technologies at the time. Today, horsepower units are used to measure the output power of numerous types of engines or motors. The electrical equivalent of one horsepower is 746 watts.
So, what’s the significance of horsepower? In vehicles, the more horsepower an engine has, the more towing capacity or speed it can deliver. If you want to increase performance in either regard, you’ll need to increase horsepower.
The same principle applies to pump motors. If you have a pump rated at 6 GPM and 1,000 PSI and you want to increase its performance, you’ll need to use a more powerful motor. Even so, a pump sprayer with a certain GPM and PSI rating won’t necessarily produce those numbers if the motor isn’t powerful enough or efficient enough. Trying to get more output out of a pump than it’s rated for without increasing the motor size will likely cause it to stall, overheat, and fail.
With vehicles, horsepower determines speed and torque. In pumps, horsepower determines flow and pressure.
RELATED: Guide to Proper Pump GPM and PSI
Why is a Motor’s Efficiency Important In Electric Pumps?
A pump’s motor ratings are more often referred to in amps rather than horsepower. A 30 amp pump is equivalent to about ¼ HP. So, the more horsepower a motor has, the more amps it will draw. When working with battery-powered pump systems, amperage draw becomes a big concern.
RELATED: The Difference Between Amps and Volts, and Why it Matters
Drawing too many amps will drain batteries quickly. Most operators want to get through an entire day on a single charge rather than swapping out batteries multiple times each day or waiting to recharge.
That’s why it’s important to pay attention to efficiency ratings on the pumps you choose for an application, as that can tell you how many amps you’re really getting. Centrifugal pumps, for example, may have efficiency ratings as low as 50%. By comparison, Pumptec plunger pumps are rated at 93% efficiency. Why does it matter?
Take, for example, a 30 amp Pumptec plunger pump (¼ HP). At 93% efficiency, you’re getting near maximum performance. If you only get 50% efficiency from a centrifugal pump, you’re only able to use 15 of those amps, or ⅛ HP. In a 50 amp motor — equivalent to ½ HP — you’d only use 25 amps or ¼ HP. The rest is going to waste.
To get similar performance ratings in a centrifugal pump as with the plunger pump, you’d have to nearly double your amperage and horsepower, meaning a bigger, less mobile pump system at a higher price tag. Even if a pump operates at 80% efficiency, that means you’re still losing one-fifth of its potential power and would have to use a larger (and more expensive) pump motor to make up for it.
Some types of positive displacement pumps are more efficient because of their simpler drive mechanism. While centrifugal pumps also have a simple drive and few moving parts, they are less efficient due to hydraulic friction. After the pump has run for a period of time, the impeller wears, the hydraulic loss is increased, and the hydraulic efficiency is lowered. Triplex oil bath pumps are less efficient due to lots of moving parts working against the resistance of the oil. The nature of a Pumptec sealed bearing plunger pump’s design is inherently more efficient.
How to Get Maximum Horsepower from a Pump System
Some pump operators believe they need a more powerful pump; that if it just had more horsepower, they’d be able to get in and out of jobs faster and get better performance.
The best way to maximize a pump’s efficiency and horsepower, however, is to optimize its flow rate.
Many pump operators purchase pumps that are actually oversized for the job. You might purchase an off-the-shelf 1.5 GPM pump but only use 1.3 GPM, meaning .2 GPM ends up going through bypass. That’s very inefficient. Ideally, you’d use a smaller motor at a lower price point and get better performance. Plus, the smaller pump would offer more mobility and longer battery life. The good news is that pumps can be customized to meet a specific flow rate for an application.
Using a pump performance chart is one way to determine your needs. An even better way is to work with a pump engineer to pinpoint the ideal GPM and PSI for your application and then design a pump solution to your specifications. To help you get started, use our free Guide to Proper Pump GPM and PSI. It outlines common standards for several industries.
Then, reach out to our pump experts. Whether an OEM manufacturer of pump equipment or a commercial business with a team of operators, we’re happy to talk through your needs and explore solutions.