Keys to Preventing Heat Buildup in High-Pressure Pumps

Shawn Glover, VP of Sales, Apr 25, 2023
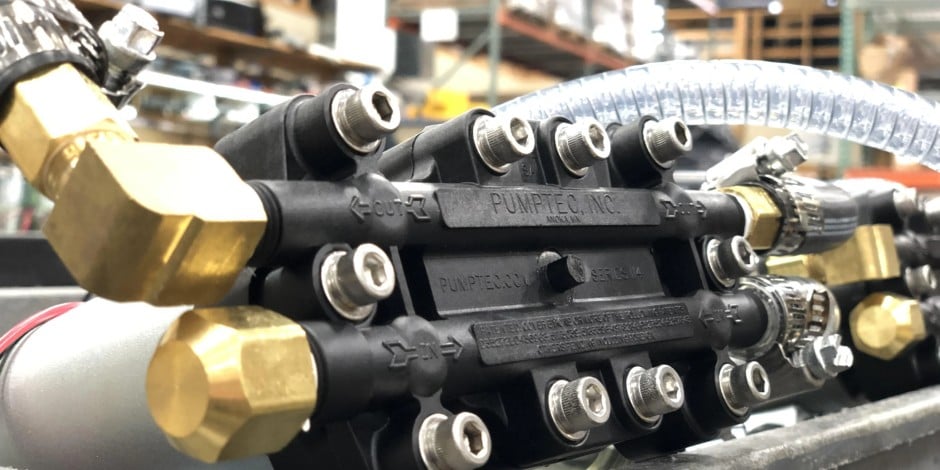
When a high-pressure pump sprayer runs without engaging the trigger, it will go into bypass mode. This is common in applications where an operator might momentarily pause spraying while moving to another area.
Allowing a power washer to run while in bypass mode for short periods of time isn’t uncommon. Prolonged periods in bypass, however, can result in extreme heat buildup that can damage the system.
Why does heat buildup occur and what can pump engineers and operators do to prevent it?
Pump Overheating Causes
Heat is the result of friction; a pump system will naturally generate heat due to the motor, bearings, and plungers going back and forth against the seal. Overheating is not limited to plunger pumps, however. Other types of high-pressure pump systems will also overheat under similar conditions.
When an operator runs a pump in bypass mode, it creates a closed-loop system that forces liquid to recirculate through the pump system again and again, absorbing more heat with each pass. Overheating issues are exacerbated with the use of a pressure regulator which keeps the pump pressurized, increasing friction. Pumps with higher flow rates like those used for soft wash and portable sanitation will also heat up faster than low-flow pumps because more heat-generating energy is produced.
Pump Damage Resulting From Overheating
Liquid flowing through a pump should never reach 140° F, as such extreme temperatures can deteriorate Viton or Buna seals and o-rings. The material becomes too malleable, almost like chewing gum, and doesn’t properly seal, resulting in leaks. Pump bodies made of PVC may also be damaged, and heated water increases the risk of pump cavitation which can destroy pump internals over time
Preventive Measures to Reduce Heat Buildup
There are numerous ways to address overheating in a pump system, including:
1. Turning the Pump Off
The simplest solution to prevent overheating is to turn the pump equipment off when not in use for extended periods of time. If you don’t plan on using your pump system for more than a few minutes, it’s best to cut power to minimize the risk and also conserve energy.
2. Reducing Time in Bypass Mode
Minimize the time your pump remains in bypass mode by engaging the trigger on the spray gun to release pressure and the heated liquid, allowing fresh water to enter the system.
3. Lengthening the Bypass Hose
By lengthening the bypass hose, the amount of water in bypass is increased, providing a natural cooling effect. The hose can be coiled up to minimize the use of space.
4. Directing the Bypass Hose to the Tank
A true closed-loop bypass returns to the inlet hose. One way to increase the amount of water in the bypass system is to redirect the hose to the water tank instead of the inlet hose.
5. Using a Pressure Unloader
A pressure unloader is a common safety device used in portable sanitation and soft wash due to high flow rates and the potential for pressure buildup, helping to reduce friction and heat buildup. While it’s still a good idea to not leave the pump running without spraying for long periods of time, an unloader can extend the time spent in bypass before damage occurs.
6. Considering a Thermal Protector Device
A thermal protector valve is another type of safety device used on some power washers, especially homeowner models that are attached to a garden hose. These accessories discharge the hot water onto the ground, allowing fresh, cool water to enter the system. Thermal valves are not conducive for many commercial applications due to the dumped water, but also because there is the potential to suck air into the system if not properly pressurized.
7. Using a Pressure Switch
A pressure switch is an accessory that detects a pump’s pressure settings and cuts power when it reaches a certain threshold. Pressure switches need to be calibrated with the system to ensure proper operation. Their settings will vary significantly from one design to another, stressing the importance of working with a pump engineer to ensure proper configurations.
At Pumptec, we work closely with equipment manufacturers and operators to ensure a pump system operates according to their specifications. Our engineers know which accessories to include and how to configure them, and we provide solid recommendations on how to reduce heat buildup and extend the life of your pump.
Contact our team of pump experts today to discuss your needs and learn more about our approach to long-lasting performance. Proper pump maintenance is another key to increasing the longevity of a pump system, so be sure to download our maintenance checklist below.