Benefits of a Variable Speed Flow Controller For Pumps

Shawn Glover, VP of Sales, Mar 30, 2021
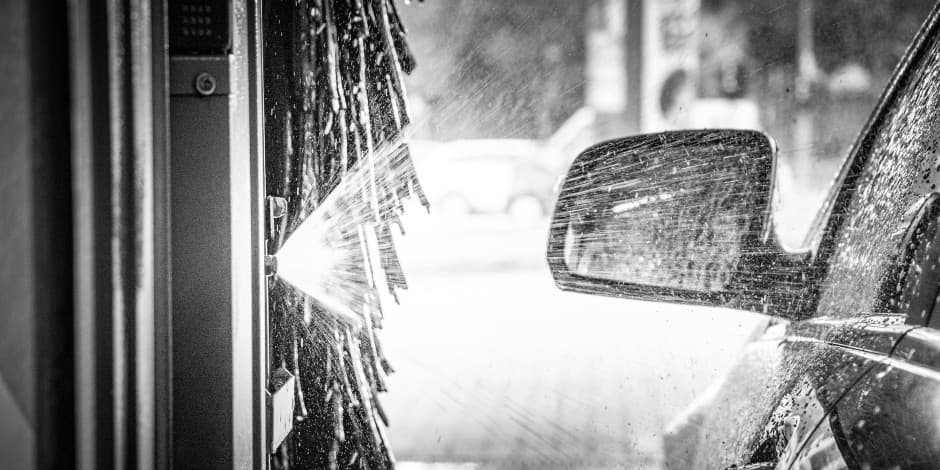
What is a variable speed flow controller and how does it help improve a pump’s performance? As its name suggests a flow controller allows an operator to adjust the output of a high-pressure pump to achieve ultra-precise coverage.
If the same rate of application is needed across multiple applications, the same pump with the proper GPM and PSI could be used for all of them. However, if the flow needs to vary up or down to achieve a very specific output, you won’t be able to make the adjustment. That is, unless you use a variable speed flow controller.
How Does a Flow Controller for a Pump Work?
A manual flow controller for a pump has a simple knob to adjust the flow up or down. With the turn of a knob, a pump operator can increase or decrease the motor speed to achieve precise output levels.
For example, if you have a 12V pump motor and use it in combination with a 12V controller, the controller can direct a new voltage to the motor that ranges anywhere from 0V to 12V based on where the knob is set. If the controller is set at 50%, it will run the motor at half speed, meaning you also reduce the flow by half while still maintaining the pressure you need.
Emerging smart technologies include automated flow controllers that use a sensor to increase or decrease the flow of fluids through a pump based on an application’s demands. For example, fertigation pumps will gauge the pH levels of a soil to determine whether it needs more or less acidification and automatically adjust the flow accordingly.
Use Cases for Variable Speed Flow Controllers
Flow controllers for pumps are ideal where outputs need to vary across multiple commercial pump applications. For example, patio misters used for cooling outdoor areas need to adjust their flow depending on the size of the coverage area. At the same time, they need to maintain pressure to produce an ultra-fine fog mist that doesn’t leave surfaces wet.
Chemical injection is an ideal application for flow controllers also. One of Pumptec’s clients provided dairy operations with sanitizing station pumps. However, each farm had different plumbing configurations in their system and different size herds. The adjustable knob on the flow controller allowed each dairy farm to calibrate the cleaning chemicals with exacting precision, ensuring that every cow received the right concentration to kill any bacteria prior to milking.
Another application is a high-pressure car wash that automatically pulls a vehicle through different wash cycles. Each stage of the wash — under-flush, cleaning foam, wax, and rinse — needs a different soap or chemical and a different PSI. Rather than purchase a different pump for each stage of the wash, a controller can be used to calibrate how much chemical is injected into each pump’s stream as a vehicle goes through the system, ensuring peak performance and a squeaky, clean car.
Benefits of Flow Controllers
As shown, the use of flow controllers offers significant benefits in many applications. Here’s a recap of how it can improve operations, along with a synopsis of additional advantages:
Precise Application
The main function of a controller is to control the flow of fluids. For industries that require ultra-precision in the application of chemicals, such as disinfection and fertigation, the addition of a controller can help dial in the exact amount of chemicals needed.
Fewer Leak Points
Because operators can typically eliminate the use of a regulator when using a controller, they can also eliminate another potential leak point. Regulators need to be compatible with various chemicals which can degrade seals over time, requiring repairs and maintenance. Typically, you won’t need a pressure safety device either because the controller has a monitor that doesn’t allow the pump to over pressurize.
Cost Savings
There’s no denying that adding a controller to a pump will increase its up-front cost, potentially doubling it. That can be a hard pill to swallow at first. What operators need to keep in mind, however, is a pump’s long-term value and return on investment.
Over time, the addition of a flow controller pump accessory can bring savings by reducing maintenance costs and product waste. It’s not uncommon for operators to end up applying 20% more chemicals than necessary because of poor flow control. If they can eliminate that waste, there’s a 20% savings right there. Additionally, if operators aren’t applying enough product, it won’t be effective and could lead to complaints and dissatisfied customers who choose to go elsewhere.
Easy Monitoring
The use of a controller allows operators to easily monitor the amount of electricity or load on a motor that is created by pressure.
Compact Size
A flow controller board can fit in the palm of your hand. At only 4” square and an inch thick, it won’t add a lot of bulk to a pump system and doesn’t protrude, making it less susceptible to being bumped around or catching on anything in tight spaces.
Does Your Pump Application Require a Flow Controller?
Pumptec recently introduced its newly engineered variable speed flow controller for use on select Pumptec pumps. If you’re curious whether your high-pressure pump application could benefit from the use of a flow controller, contact our pump experts and we’ll be glad to talk through your needs and customize a solution for you.
Also view our Guide for Proper GPM and PSI below to help ensure your system is performing in accordance with various industry standards.