Find the basic outline of a sprayer/ag, common issues, and best practices for the system.
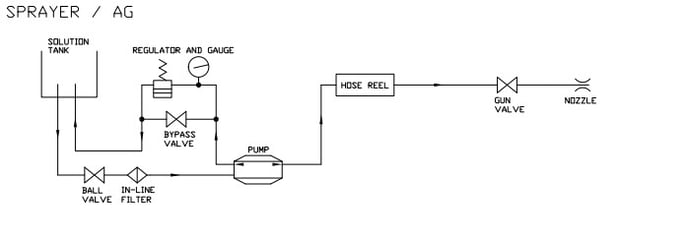
Shown above is a basic sprayer/ag system. In the diagram you can see the pump pulls water from a solution tank through a filter and sends the water through a hose and out to the gun and nozzle. A second outlet is used to regulate and check pressure while by-passing the excess fluid back to the solution tank. Here are a few things to take note of, avoid, and help to make your system the best it can be.
Firstly, the pump you use matters. To reach the desired pressures and flows your system needs, and also considering voltage and amps, please visit this page to view Pumptec's options based off of your needs. Second, the pump needs enough water. Do not run the pump dry, make sure your hoses are properly sized, and all connection points are water tight. We typically recommend using 1/2" S-hose to feed pump inlets, Pumptec pulse hose for pressurized outlets/sections of the system, and 3/8" to 1/2" S-hose on by-pass lines. These hoses keep great shape and allow enough flow. Starving the pump will lead to cavitation. These hoses easily connect with the needed strainers and filters between tank and pump. In some instances, it would be appropriate to pressure-feed the system using city water sources.
Once the fluid leaves the pump, it is imperative to use a dampening hose. At Pumptec, 3/8" pulse hose is widely used. Because of the high operating pressure and the nature of our plunger pumps, the outlet hose type is extremely important to functionality. Be sure to always double check that your inlet and outlet hoses do not get pinched or damaged so as not to overpressure or run the pump dry. Do not run your by-pass line from the regulator directly back to the pump as this could contribute to cavitation and overheating. Run it back to the solution tank as shown in the diagram above. Over-pressuring can also result from the incorrect regulator pressure limit. Pay attention to your gauge, so you do not over-amp your motor or over-pressurize your pump.
Pest spraying can have specific chemical usage requirements and application pressure limits, so use the included information as a guide only. Refer to label requirements for each specific chemical. When choosing a pump for spraying, pressure loss in the hose must be considered. The pressure is greatest at the pump and decreases over the length of the hose. Typically, these systems utilize very long hoses, 200-300 ft. is common, and requires a certain minimum amount of performance to move the flow through the lengths of hose. For example, a 3 GPM system will require (lose) 50 PSI per 50 ft. of 3/8” ID hose. A pump with only 60-70 PSI may not provide the desired performance at the end of the hose. See reference charts to assist in system design.
To reiterate, avoid starving or running the pump dry, pinched lines, incorrect pressure limits or pressure spikes, overworking the motor and/or pump, and overheating your water, pump and/or motor. Avoiding negative head pressure is also preferrable - this means that the solution tank the pump is drawing from is placed above the pump. One last thing to look for is a dysfunctional nozzle - they may be damaged, worn out, or clogged.
Normal check ups and maintenance checks are recommended on all pumps, hoses, fittings, and nozzles. Below are a few helpful links regarding sprayers/ag units, pump maintenance, and more.
Helpful Links:
Understanding Pump Flow Rate vs. Pressure and Why it Matters